The heat dome reached us all the way up here, in the northeast corner of the country. There was no reprieve from it on Tuesday, not even beside the ocean, which is usually significantly cooler than at the shop.
We’re making rocking chairs this week, and we’re about half way through the chair. And we’re taking a few more breaks than usual this week. (I realize, southern states, that you deal with this weather all summer long.)
Two thoughts have been running through my mind. One prompted by a student question. The other is something I realized last week as I made one final push to remove debris and “wood with future potential” from the shop before a group of chairmakers joined the space for a week of rocking chairs. This is the first class in the shop in about eight months… plenty of time for extra stuff to accumulate.
Within each corner of the shop are stashes of riven red oak. Just oddball stuff, squirreled away, awaiting a decisive moment of action. Will that material be chopped up and placed in the firewood stack? Or is it a chair rung? And then it hit me…this wood, tucked into the corners, it must pass a simple, stupid question. One that I ask myself when holding each riven piece:
“Is this a stick?”
The shortest common rung used in the chairs is around 14” long by 3/4” x 3/4”. The squirreled material may have a stick or two in it. I’d like to extract that stick from clear red oak whenever possible. It’s usually a rainy day activity and that day may take months to appear. Or an upcoming class may force some action.
Of those in the pictures, the triangular shaped pieces are most likely to become winter warmth. The triangular shaped is material that resides near the pith of the tree and the wood is often wavy, bowed, and twisted. There may be a rung stick hiding in them, but these parts often heavily distort upon entering the drying kiln, even if they shave nice and straight. I’ve become more wary of this material.
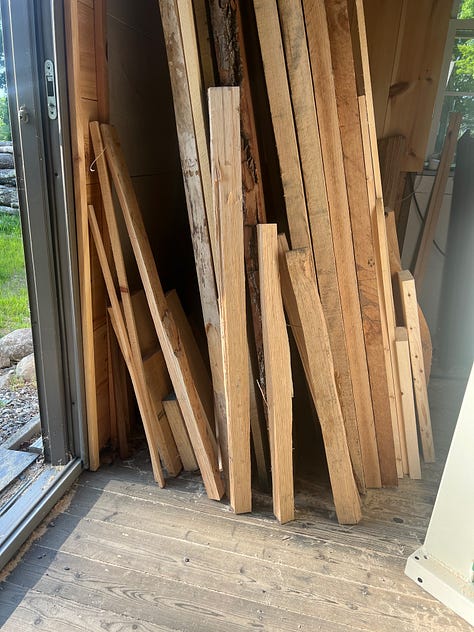
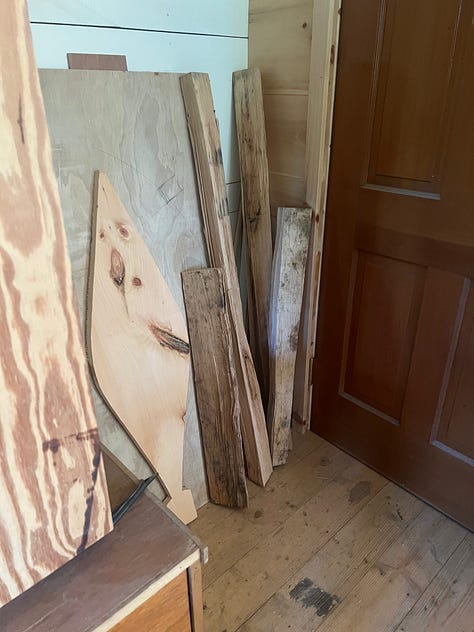
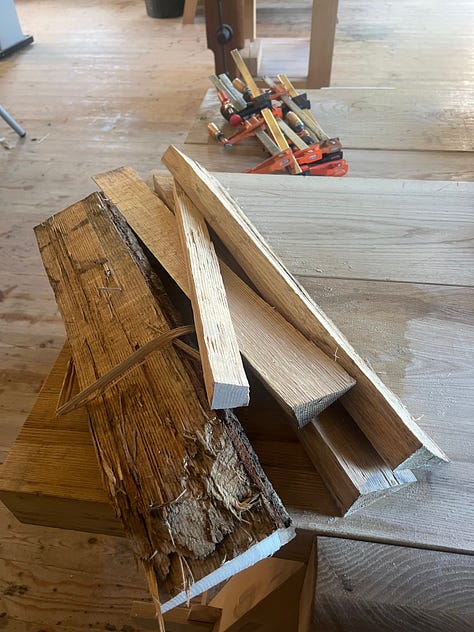
Second thought… A few days ago, a student asked, “What’s your favorite chair?” Picking just one is tough, so I went with instinct and the first idea that flashed across my mind.
I sat with the question a moment, then settled upon Brian Boggs’ Berea Chair. I’ve always loved that chair. Even before I started making chairs, or making furniture at all, I somehow knew of that chair. Researching for the book only deepened my appreciation - both of Boggs and his chair.
First, the chair is gorgeous. It’s robust, delicate, and comfortable. The silhouette is spot on. And it looks good from all angles (not all chairs pass this critique). It marries traditional and contemporary ideas. I hope to own one someday.
Favorite details: 1) the pyramid slat pegs. 2) Rake and Splay. Adding it to the ladderback makes the chair. 3) Treatment of the hickory bark. The bark seat is refined and polished. It takes bark beyond anything I’ve seen before. The bark tapers from wider at the front rung to narrower at the back, which fills in the widening flair of the chair front and eliminates the need for filler strips.
Second, Boggs worked on that chair for decades to get it to that point. He refined it to the point of completion. That’s inspiring, at least to me, to consider working on a chair idea until it’s so “right” that there’s no moves left…no changes or tweaks or versions or improvements to consider. Maybe, hopefully, decades from now I will have a similar experience with a chair that I make.
Third, and I like this piece as well, was that Brian stopped making them because there were other chair ideas to pursue and shared them with the woodworking community. Other fine chairmakers now make and teach the Berea Chair (Eric Cannizarro, Jeff Lefkowitz, and David Douyard are a few that come to mind). The Alexander Brothers sell material kits to build the Berea Chair. Mr. Lefkowitz sells a manual, with the procedure and fixture construction details. The chair had commercial success in Boggs’ shop and is a popular chair within the woodworking community.
I’ve yet to sit in a post and rung chair as comfortable as Brian’s Berea chair ❤️
I've built three of the Boggs chairs so far. I'm working on a dining room set. They are the most comfortable and beautiful I've found so far. Jeff's plans make it pretty much idiot proof.
It's allowed me to experiment with bending. I use lumber yard kiln dried cherry, walnut, and curly maple, and they've all bent just fine. Of course I chose the stock very carefully for straightness of grain. I've got all the legs bent for the rest of my set. I just need to get ahead on other work before I get back to it.