But before I jump into the Windsor chair, please allow a short aside;
The word “bespoke.”
About 5-10 years back, it seemed like this word popped up everywhere within the craft world. Since I’m most attuned to the woodworking scene, I noticed it attached to custom furniture and the work of furniture makers. I didn’t use the word in any web or social media posts (because of my own confusion over it’s use and meaning, more than any other reason). I don’t chide any furniture makers who uses it. It’s the right word in many instances. A person can only use the phrase “hand-crafted” so many times when attempting to market and #hashtag their work.
Though at this point, the word has moved well beyond the craft community.
A few years ago, McDonald’s began selling “bespoke sandwiches.” I remember giggling whenever that ad campaign came on the radio. And yesterday, while listening to music on Spotify, an ad for Samsung’s “bespoke refrigerator” tried to persuade me to purchase a major appliance during Lowe’s 4th of July sales.
For some reason, I absolutely love the phrase “bespoke refrigerator.” When I first heard it, I stopped working at my bench (job well done, advertisers) and did a mental doubletake. “Did I hear that right…bespoke refrigerator?” And then I envisioned refrigerator hipsters working away. Then selling their refrigerators at a trendy, local shop. A trendy, local shop like Lowe’s. It was a fun mental exercise.
I’m already looking forward to the next ad campaign at uses the word. Maybe State Farm can sell “bespoke insurance” during football season. [please make this happen…I cheer for the Cleveland Browns and could use a reason to smile during the games].
Alright. Onto the furniture.
I’m well into Make a Windsor Chair with Mike Dunbar at this point. The primary objective is the book review…that’s what got this project started. But there’s a second reason, just under the surface. I’d like to make a chair with Mike Dunbar.
I missed out while he ran the Windsor Institute. Too late on my part. As I teach more chairmaking courses here in New England, I find that my students have often taken a class in New Hampshire with Mr. Dunbar. And they relay their positive experineces. I wished I’d have gotten in on it.
Another reason: I’m attempting to be a student again. I’m attempting to turn off my “auto-pilot” chairmaking instincts and preferences, and to learn from Mr. Dunbar’s methods. It’s not an easy thing to do and I have more empathy for my students because of it. I’ve written/complained here on Substack before about how students interrupt me during a demonstration to say, “that’s not how I do it.” Well, I’m saying those same things while reading through Mr. Dunbar’s book. I’ve asked my mental dissenting voice to stay silent as I attempt to follow directions.
Last reason: I don’t have many professional development opportunities throughout the year. This is one of them. I know Mr. Dunbar uses different methods than I employ when building a chair, so I’m going to his book to experience new ideas and approaches.
As for the chair itself, it starts with the seat and turnings. I’ve used air dried white pine for the seat blank and fresh ash for the turnings. I went with the bamboo turnings instead of baluster. [I didn’t want to source wood, and I have the fresh ash. If maple or birch were available, I’d make the baluster turnings. Fine-grain woods do a much better job with the fine details found on balusters.]
The seat. I set about shaping it…and quickly found that my travisher was no match for the pine. My travisher has shaped a handful of stick chairs recently, with their oaks seats, with only a quick hone or strop between each seat. This was different. The soft pine tore in all directions. A dull tool can handle harder woods easier than soft. After a full resharpening, the travisher sliced away the bowl with minimal tearout.
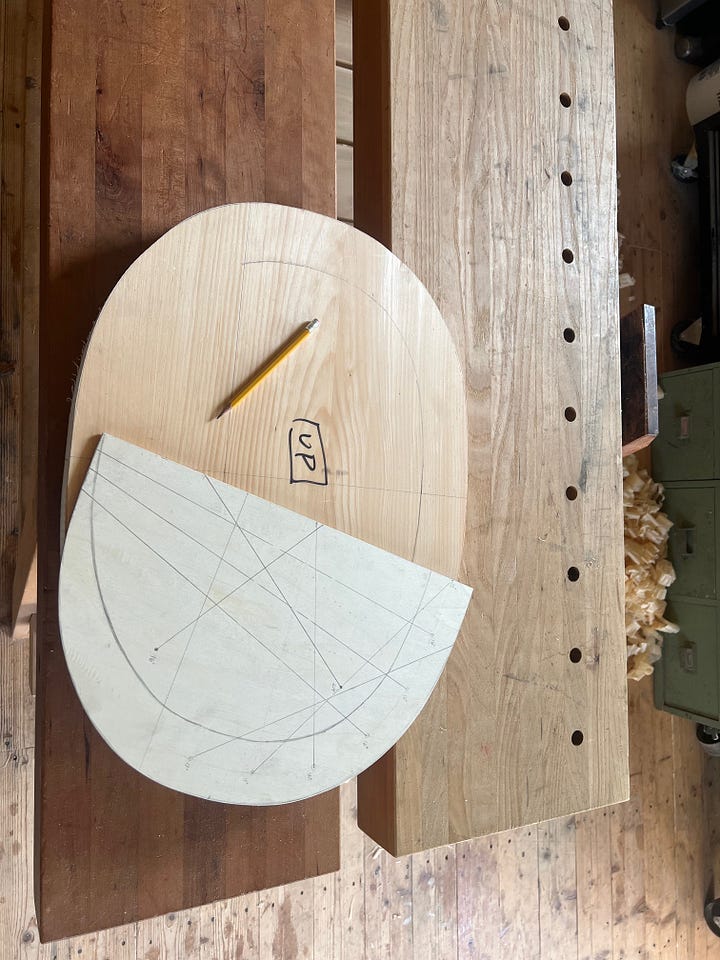
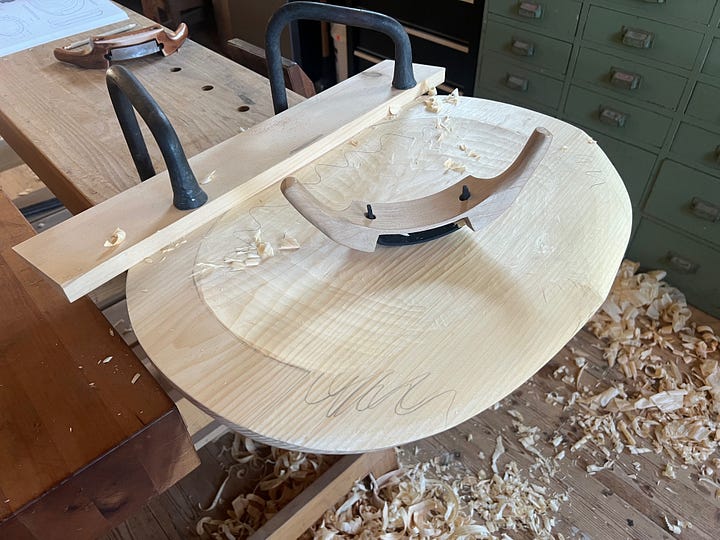
Then it was onto turnings. This was my first opportunity to use the carving vise. After riving oak billets for turning stock, the parts went to the vise to knock off corners in preparation for the lathe. [It’s much easier, faster, and more enjoyable to turn a rough octagon at the lathe than to battle with the corners of “square-ish” stock. When turning wet wood, strands of corner material often fly off, slapping at the hands or being flung towards the turner’s face. Better to take off the corners before mounting the piece on the lathe.]
My first impression of using the standing vise instead of the shave horse… I like it. It allows for more freedom of movement than the horse. I placed the blank into the jaw, then comfortably took down both corners. It was an action that would not have been possible in the shave horse, due to the restrictions of that piece of equipment.
I have more parts to make at the vise. All the spindles, along with the bow and arm rest. Now that I’ve done some bulk work at the vise, I’m wondering how it handles the more delicate and detailed parts of the chair. I’ll find out soon.
One future change for the vise… I mounted it to one of the Moravian workbenches here in the shop. I’m guessing the bench weighs around 200 lbs. Doing the heavy stock removal of the ash leg blanks caused the bench to follow me around the room. The bench danced and moved. This would be an issue with any of the benches I have in the shop. I need to either add weights to the shelf area, or I need to affix the carving vise to a bench that’s tied to a shop wall. Something more is needed to keep it in place. But that’s a future issue.
Now, another test for the vise. The long, delicate back and armrest…
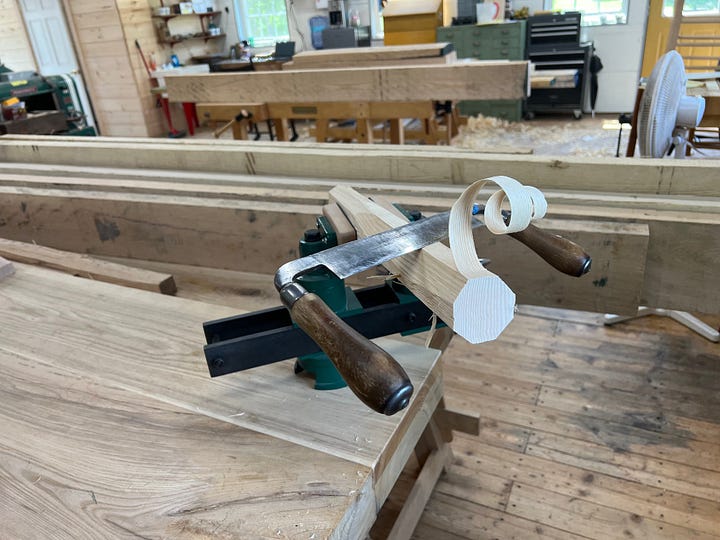
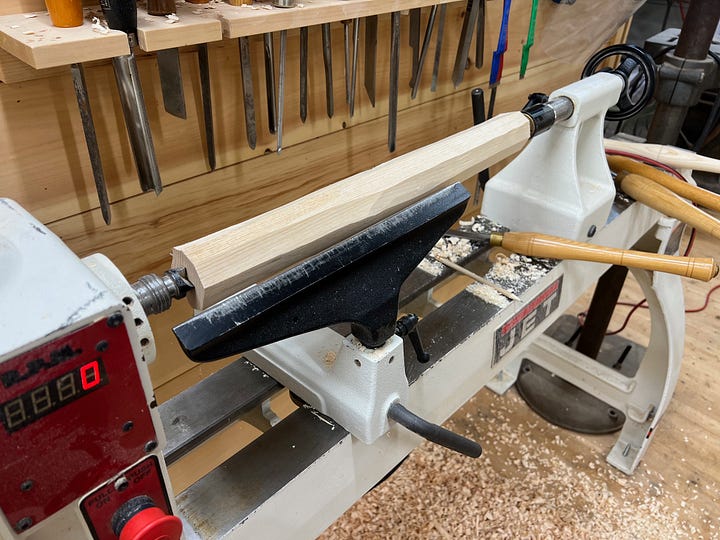
Between you and watching videos of Elia Bizzarri and Curtis Buchanan, you're making me want to make a Windsor chair. I guess I need to add that to my list of things to do...
Thanks for doing this!
Re: the bench moving, I use a lighter English style bench, and I’ve started using my foot to stop it from moving. The same way when using a shave horse the pulling causes you to push hard on the peddle, and so tighter on the stock, I use my foot to brace one of the legs, so when I pull with the drawknife it pushes on the leg. It still hops sometimes with real heavy cuts, especially in the tangential plane but overall a simple fix. Works great when using the leg vise too to shape material